Chandimal Adikari
In today’s world most ofthe goods we purchase come from outside of our own area. Have you ever wonderedhow these items get to your hands from the producer?
The system of getting goods to your hands from the producer is known as “the supply chain”.
This is actually an over simplification of supply chain and supply chain related activities. Asupply chain can be as simple as buying an orange which was just plucked from atree or as complex as assembling an airplane with parts manufactured in several countries. Along this train of thoughts, it is easy to see that everything hasits own supply chain.
What is logistics?
Delivering goods to your hand is one of the major tasks of a supply chain. This "delivery" isdone by transporting goods by many means. Transportation and transportation-related activities in a supply chain can be called “Logistics”.
There are two majorforms of Logistics.
1. InboundLogistics - Transporting goods to a factory or warehouse
2. OutboundLogistics - Transporting goods out of a factory or warehouse
These Logisticsoperations contribute to a major cost component of the supply chain. It cancome up to more than 50% of the overall supply chain cost.
How to reduce the cost oflogistics?
Transportation cost isdirectly associated with the number of vehicles used to move the goods and their mileage. Higher the number of customers we reach out to, higher the number of vehicles that leave our factories and warehouses, and the mileage they cover. It will also increase the number of vehicles which deliver raw materials to our factories.
We can't make logistics cost ZERO by halting all the transportation activities!
Then how can we reducethe transportation cost? The answer is clear; it is by lowering the number ofvehicles and their mileage.
How can Digitisation help withthis?
In theory, we can reduce the number of vehicles needed, by consolidating multiple deliveries into one.
Does this mean that ifwe converge all the deliveries into one vehicle, it will be cheaper? Yes and No. Let’s look at the following example:
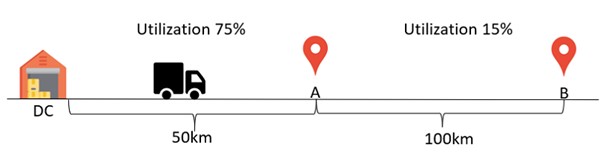
If a vehicle is loaded with 2 orders - one is 6000kg (Point A) and the other is 1500kg(Point B). But the distance from Distribution Centre (DC) to point A is 50km and to point B, it is 100km. Even though the vehicle is 75% utilised- space orweight wise - after unloading the goods at Point A, it will drop down to 15%. Then the vehicle, an almost empty truck, goes another 100km to Point B.
In instances like thissending two separate small vehicles can be cheaper than sending one large vehicle with both orders. It is not easy to correctly identify these situations when the number of orders increase.
Let’s take an example of3 deliveries A, B & C. These deliveries can be arranged in the following manner.
{{A,B,C}} , {A,{B,C}} ,{{A,B},C} , {B,{A,C}} , {{A},{B},{C}}
After considering factors like vehicle loading capacity, location of the delivery points, vehicle handling problems at delivery points etc. we can eliminate some of them. Then we can select an option which costs us the least.
However, with the increase in the number of orders, possible ways to arrange the orders will increase exponentially.
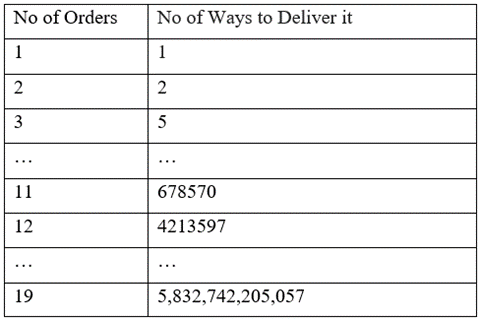
Large organisations get hundreds and thousands of orders per day. Therefore, a mathematical solution isneeded for this problem.
Transportation Management Systems (TMS) with transportation planning functions can help bycomparing options. A transport/ logistics management system is smart enough toprovide dynamic solutions for fast-changing consumer patterns with the help ofmachine learning.
One Step Further…
The utilisation of avehicle can be measured mainly in two methods.
3. Compared tothe maximum weight it can hold
4. Compared tothe maximum volume of goods it can hold.
For example, a milkcarton is heavier than a bag of chips that has the same volume. If we receivean order for 1,000 milk cartons and 1,000 bags of chips from the same buyer, wecan put all the milk cartons in one vehicle and there will still be space left.However, by weight, the vehicle can be utilised up to a 100%. Also, if we try to load all the bags of chips to another vehicle, some bags may have to be left behind due to the space restriction. Hence another vehicle will be required.
Nevertheless, there is aproduct mix which permits the use of only two vehicles. Both vehicle spaces andweight capabilities will be utilised. With two products it will be easier tofind the proportions to get the maximum out of both vehicles. When the numberof products increase due to heightened demand, it will get harder for obtain this optimum product mix. This is another occasion where an Intelligent Transport Planning Application can help.
Final Words
Considering these cases,it is clear that digitising logistics planning in supply chains will help reduce the cost of logistics. This article is majorly focused on OutboundLogistics. However these situations are also applicable to inbound logistics aswell since one’s inbound logistics is someone else’s outbound logistics.
If you are interested inthis, I have co-authored a research paper where you can study more about this.